The hot-dip galvanizing technique consists of three main stages: surface preparation, galvanizing, and inspection. The specifications for the process are determined based on ASTM International standard specifications for hot-dip galvanizing of iron and steel products.
The steel components are first placed in baskets or fixed to specially designed fixtures. If the component has gone through previous procedures that require lubrication, such as rolling, bending, or drilling, a pre-degreasing process might be applied before the material goes through the degreasing/cleaning stage.
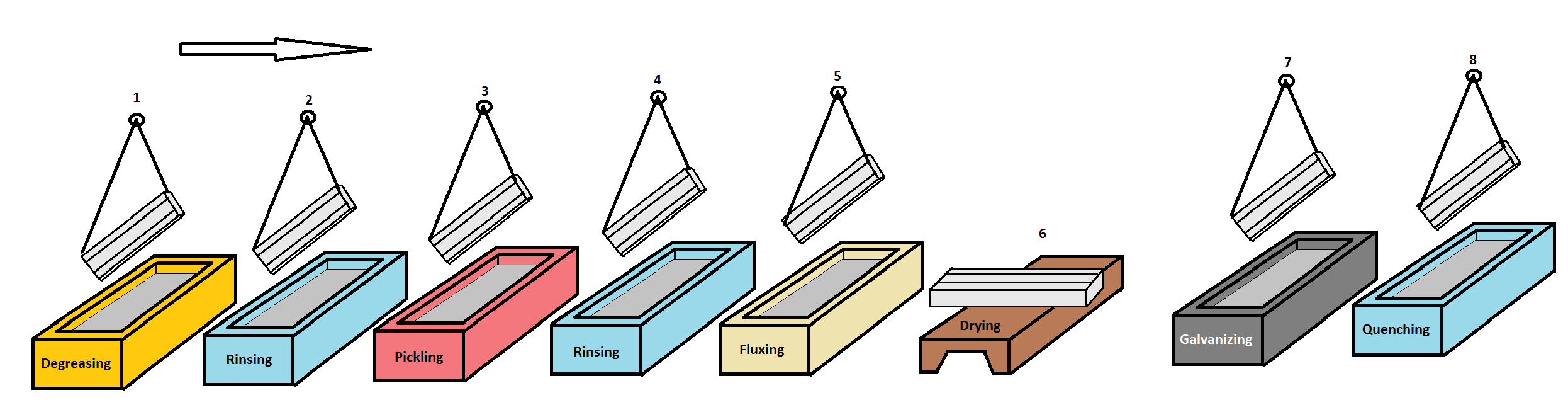
Step 1: Surface preparation
Surface preparation is the first and essential stage of hot-dip galvanizing. Without proper surface cleaning, the necessary reactions between the steel surface and zinc will not take place resulting in the discontinuity of the coating and failure of the galvanized product.
The surface preparation process involves two or three main steps depending on whether wet or dry hot-dip galvanizing technique is employed. Wet hot-dip galvanizing involves degreasing and pickling, while dry hot-dip galvanizing includes an additional fluxing step in which the component is transferred to a flux bath after degreasing and pickling.
During the degreasing process, the steel component is submerged in a bath of either hot alkali solution, such as caustic soda at 70-90 oC, mild acid, or biological cleaning solution. This process removes dirt, paint markings, grease, oil and other organic contaminants from the surface of the material. The immersion duration depends in the degree of contamination. However, a typical degreasing duration of 5-10 mins is usually enough. Furthermore, a slight agitation of the cleaning solution during submersion can increase the efficiency of the process.
Additional contaminants, such as epoxies and welding slag, which cannot be cleaned during this step, should be removed by a mechanical process, e.g. sand blasting. The degreasing step is followed by rinsing the component in water.
The second step of surface preparation involves pickling, in which the material is submerged in a bath of hot (60-70 oC) diluted sulphuric acid solution or ambient hydrochloric acid solution to remove mill scale and rust. The acid concentration is chosen based on the degree of oxide scale present at the surface of steel component; however, a solution of 10-20 Vol.% is normally enough to remove the excess scale and rust. Since there is a good chance of pitting at the component surface as well as an accelerated destruction of the pickling kettle, inhibitors are also required in the bath in order to ensure that the component and the pickling kettle are protected against corrosion.
A mechanical cleaning process, such as abrasive cleaning, or air blasting of sand or grit, can also be used along with, or as an alternative to chemical pickling. This step is also followed by rinsing in water.
It is worth mentioning that an improper pickling step can significantly reduce the quality of the protective coating. In addition, the excess amount of scale and rust, which are not removed during the pickling process, enter the galvanizing bath and increase the amount of zinc ash/dross, hence increasing the consumption of zinc and decreasing the efficiency of the galvanizing process.
If a wet hot-dip galvanizing technique is used, the steel component is transferred to the galvanizing kettle straight after pickling. In the case of dry galvanizing method, the pickled component is submerged in a bath of zinc ammonium chloride solution. This process removes all the residual oxides from the steel surface and allows for a thin protective layer to adhere to the surface in order to prevent the reoccurrence of oxides prior to galvanizing. The fluxing is followed by drying the component at ~ 120 oC.
Step 2: Galvanizing
Once the surface preparation is complete, the clean component is transferred to a galvanizing kettle and immersed into a molten zinc bath. The temperature of the molten zinc bath is usually kept at ~ 450 oC, which is about 30 oC higher than the melting point of zinc. Such high temperature of the molten zinc allows for higher fluidity and better adherence to the steel surface. During the submersion of the component, the molten zinc reacts with iron at the material surface and forms several layers of zinc-iron intermetallic alloys. The outmost layer of the coating normally consists of pure zinc.
After the completion of the galvanization process, the galvanized products are withdrawn from the bath and the excess zinc is removed via draining, and vibration, as well as centrifuge for small pieces, such as nuts and bolts.
The components are then quenched in water. If the cooling is not done fast enough, the mutual diffusion of zinc and iron atoms results in the Kirkendall effect (the motion of the boundary layer due to the difference in the diffusion rate of zinc and iron atoms), which can cause pitting and scaling of the zinc coating.
Step 3: Inspection
Once the galvanized products are cooled down to room temperature, any residual zinc remained on the surface of the product is removed by proper methods, such as filing. It is noteworthy that excess filing can cause damage to the coating. Another issue is removing the traces of excess zinc that remain on the product surface. Any discontinuity of the zinc coating should be mended with the permission of the producer and based on ASTM International standard practice for the repair of damaged and uncoated areas.
The galvanized products should be transported inside moisture-free containers and the components must be packed separately so that air can flow in between the gaps at all times.