تست سالت اسپری، یا تست مه نمکی، یک روش سریع برای آزمایش میزان مقاومت به خوردگی محصولات گالوانیزه است. هدف از انجام این آزمون، بررسی خواص خوردگی فلز گالوانیزه شده تحت شرایط آزمایشگاهی و تخمین عمر قطعه در شرایط واقعی کاربری است. محققان سال ها از این آزمون به منظور بررسی و توسعه پوشش های فلزی و رنگی، عملیات های شیمیایی و … استفاده کرده اند.
در تست سالت اسپری از یک محلول حاوی 5% نمک (کلرید سدیم) در آب استفاده می شود. این محلول به طور مداوم و به شکل مه بر روی سطح قطعه اسپری شده و آن را همواره در معرض خوردگی قرار می دهد. قطعه معمولاً در داخل محفظه به طور مرتب دوران داده می شود تا تمامی سطح قطعه به طور یکنواخت به محلول نمک آغشته شود. دمای داخل محفظه در حین انجام تست ثابت نگهداشته می شود. جزئیات این آزمون در استاندارد بین المللی ASTM B117 تشریح شده است.
با توجه به اینکه تست سالت اسپری تنها یک تخمین کیفی از سنجش مقاومت به خوردگی پوشش گالوانیزه است، هیچ معیار مشخصی در استانداردهای معتبر بین المللی، از جمله استاندارد ASTM، جهت تعیین عمر کاربری قطعات گالوانیزه شده بر اساس نتایج این تست ارائه نشده است. در متن استاندارد ملی INSO 16353 گالوانیزه گرم نیز آمده است: ” نتایج آزمون خوردگی کوتاه مدت (مانند آزمون مه نمکی و آزمون کسترنیک در استاندارد ISO 6988) نباید برای پیش بینی عملکرد خوردگی پوشش گالوانیزه در درازمدت مورد استفاده قرار گیرد.”
بعلاوه استاندارد ASTM B117، که به تشریح روش انجام تست سالت اسپری می پردازد، در مورد مدت زمان انجام آزمایش و نحوه تحلیل نتایج تست هیچ گونه اظهار نظری نمی کند و انجمن گالوانیزهکاران آمریکا نیز انجام این تست را جهت سنجش عملکرد پوشش گالوانیزه توصیه نمی کند.
انجمن بین المللی روی در مورد اعتبار تست اسپری نمک میگوید: ” هدف از انجام هر نوع تست خوردگی تسریع شده، شبیه سازی عملکرد خوردگی یک محصول در محل کاربری آن است. برای اینکه یک تست خوردگی تسریع شده عملاً قابل استفاده باشد، باید بتوان نتایج آن را با عملکرد تحت شرایط واقعی مطابقت داد، اصلی که هرگز در مورد تست اسپری نمک محقق نشد.” به همین علت نیز بسیاری از محققان به این نتیجه رسیدند که تست سالت اسپری هیچ ارتباطی به عملکرد خوردگی ندارد و انجام این تست باید متوقف شود.
در طول سال ها، چالش های زیادی در مورد اعتبار دادههای تست سالت اسپری به وجود آمده است. مسلماً قطعات گالوانیزه شده در بسیاری از محیط های کاربری در معرض مواد شیمیایی نمکدار قرار نمی گیرند و حتی اگر هم قرار بگیرند به ندرت اتفاق می افتد که در چنین غلظت بالایی از نمک (5 درصد برای تست اسپری نمک) قرار بگیرند. طبق استاندارد ASTM B117، یک رابطه مستقیم میان مقاومت به اسپری نمک و مقاومت به خوردگی در سایر محیط ها به ندرت دیده می شود؛ زیرا شیمی واکنش ها، از جمله تشکیل فیلم ها و قدرت محافظت کنندگی آنها، بسته به شرایط محیطی شدیداً تغییر می کند. بنابراین این سؤال مطرح می شود که تست سالت اسپری تا چه حد اعتبار دارد؟
به عنوان مثال، یک فولاد گالوانیزه شده در محیط های سولفیدی نسبت به محیط های عاری از سولفید نرخ خوردگی بیشتری دارد. از طرف دیگر، واکنش های خوردگی در یک اتمسفر کلریدی مشابه یک اتمسفر سولفیدی نیست. در نتیجه، نباید انتظار داشت که نتایج تست سالت اسپری با عملکرد واقعی قطعه در محیطهای سولفیدی مطابقت داشته باشد. بعلاوه، سازندگان توصیه می کنند که قطعات فولادی گالوانیزه شده برای کاربردهایی که قطعه باید تمام مدت در معرض رطوبت قرار داشته باشد استفاده نشوند، و این در حالی است که در تست سالت اسپری، قطعه به طور دائم در یک محیط بسیار مرطوب آزمایش می شود. در واقع، عملکرد مطلوب پوششهای گالوانیزه نیازمند خشک شدن سطح پوشش ها بعد از خیس شدن است و نیاز به این سیکل های خیس/ خشک در پوشش های گالوانیزه پدیدهای شناخته شده است. علت نیاز به خشکی این است که وقتی سطح پوشش خشک می شود، لایه فیلم اکسیدی و یا کربناتی پسیو و نسبتاً پایدار روی سطح تشکیل می شود که لازمۀ عملکرد مناسب این پوشش ها در برابر خوردگی است. زمانی که پوشش به طور دائم در طول تست اسپری نمک خیس است، امکان توسعه این لایه پسیو اکسیدی/کربناتی وجود ندارد.
یکی دیگر از اشکالات تست سالت اسپری این است که نتایج از یک قطعه به قطعه دیگر مشابه آن خیلی متفاوت بوده است. دو قطعه کاملاً یکسان که به یک روش کاملاً مشابه هم اما در دو کابین مختلف تست میشوند نیز در بسیاری موارد نتایج کاملاً متفاوتی را نشان داده اند.
دلایل بسیار متعددی برای عدم تطابق تست سالت اسپری با عملکرد پوشش های گالوانیزه تحت شرایط واقعی وجود دارد که سه مورد از مهم ترین آنها عبارتند از:
- سطح قطعات تست شده دائماً خیس بوده و سیکل خیس/خشک به آن اعمال نمی شود، در حالی که در شرایط کاربری این طور نیست.
- غلظت کلرید، 5 درصد است که غلظت بسیار بالایی بوده و از تشکیل یک لایه پسیو توسط روی جلوگیری می کند، در حالی که عملاً حین کاربری، این لایه تشکیل می شود.
- نتایج تست از یک قطعه به قطعه دیگر مشابه آن و از یک کابین تست به کابین دیگر بسیار متفاوت است.”
بنابراین بر اساس اظهار نظر انجمن گالوانیزهکاران آمریکا، انجمن بین المللی روی و استاندارد ملی ایران، مجموعه ارک نوین نیز انجام تست اسپری نمک بر روی پوشش های گالوانیزه را توصیه نمی کند. اما چنانچه کارفرمایان محترم در انجام این تست مصر باشند، مطابق با آنچه در استاندارد ASTM B117 ذکر شده باید در مورد نحوه و مدت زمان انجام تست و نیز چگونگی تحلیل نتایج آن بین کارفرما و گالوانیزهکار توافق دو طرفه صورت بگیرد.
طبق پیشنهاد (و نه دستورالعمل) انجمن بین المللی روی، عملکرد خوردگی قطعات گالوانیزه شده در حین تست اسپری نمک، که مطابق با استاندارد ASTM B117 انجام می گیرد، را می توان به روش های زیر ارزیابی نمود:
- تعداد ساعات تا بروز اولین اثرات زنگ زدگی فولاد یا همان زنگار قرمز؛
- تعداد ساعات تا وقتی که 5 درصد مساحت سطح قطعه دچار زنگار قرمز شود؛
- تعداد ساعات تا 10 درصد زنگار قرمز سطح قطعه؛ و …
مشاهده اولین نشانه های زنگار قرمز در سطح فولاد گالونیزه شده به این معنی است که پوشش روی در نتیجه واکنش خوردگی به طور کامل از بین رفته و خوردگی به زیرلایه فولادی رسیده است. در این تست هیچ معیار یا محدوده ای که نشاندهندۀ بهترین عملکرد خوردگی باشد وجود ندارد و تنها به تعریف مصرفکننده از “مردود شدن” بستگی دارد. جدول زیر یک راهنما است که اغلب به عنوان معیاری برای تخمین عملکرد پوشش گالوانیزه گرم شده مورد استفاده قرار می گیرد.
جدول راهنمای مقاومت به تست اسپری نمک برای یک پوشش گالوانیزه گرم شده [International Lead Zinc Research Organisation]
محصول گالوانیزه شده | ضخامت معمول پوشش در هر طرف، µm | تعداد ساعات تا 5% زنگ زدگی | |
در هر میکرون ضخامت پوشش | برای ضخامت معمول پوشش | ||
گالوانیزه (پوشش روی) | 20/5 | 10 | 205 |
گالوان (پوشش روی-5% آلومینیم) | 21/5 | 25 | 540 |
گالوالوم (پوشش 55% آلومینیم-روی) | 21/5 | 50 | 1075 |
داده این جدول نشان می دهد که به عنوان مثال، برای قطعه ای با ضخامت پوشش 20/5μm، زمان نقریبی تا بروز 5 درصد زنگ زدگی قرمز در تست اسپری نمک حدود 205 ساعت است.
یک استاندارد جایگزین برای استاندارد معمول ASTM B117 استاندارد ASTM G85 است که شامل اصلاحاتی در انجام تست اسپری نمک، از جمله افزودن سیکلی اسید و SO2است؛ هر چند که این استاندارد به اندازه استاندارد ASTM B117 مورد استفاده قرار نگرفته است.
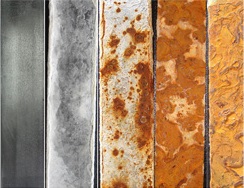
با توجه به دیتاهای جهانی جمع آوری شده عملکرد خوردگی پوشش گالوانیزه طی سال های طولانی، نرم افزاری به منظور تخمین دقیق تر و واقعی تر نرخ خوردگی روی در محیط های گوناگون توسعه یافته و انجمن گالوانیزه کاران آمریکا نیز بکارگیری این نرم افزار را توصیه می کند. جهت کسب اطلاعات بیشتر در این زمینه به دو لینک زیر مراجعه فرمایید:
http://www.galvinfo.com:8080/zclp/